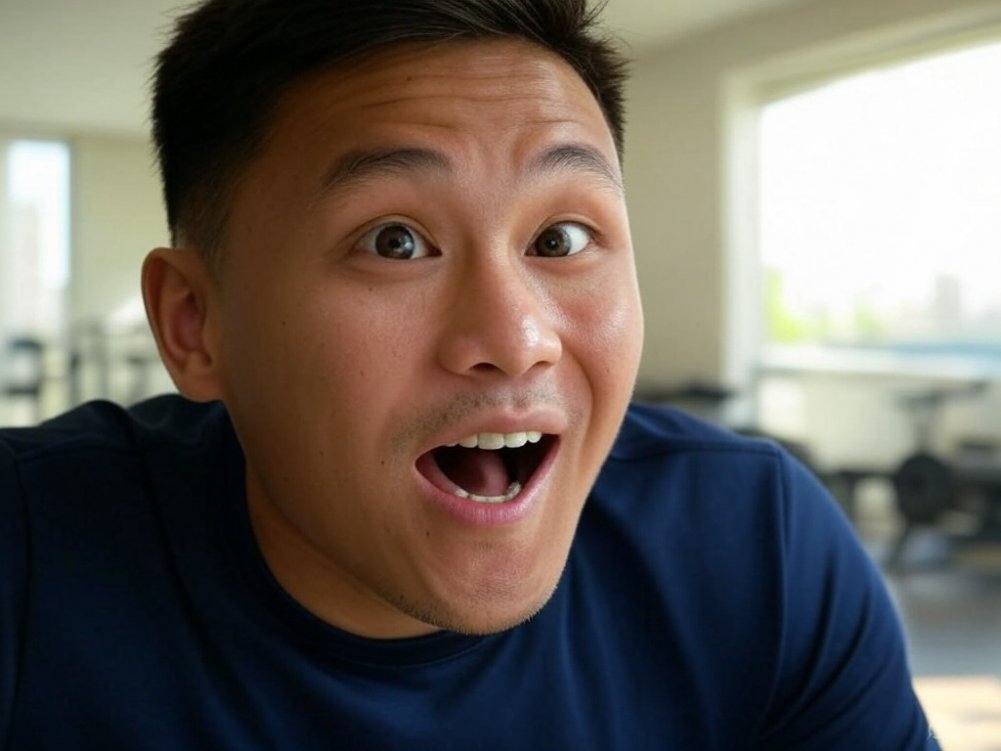
Introduction to Modern Pump Innovations
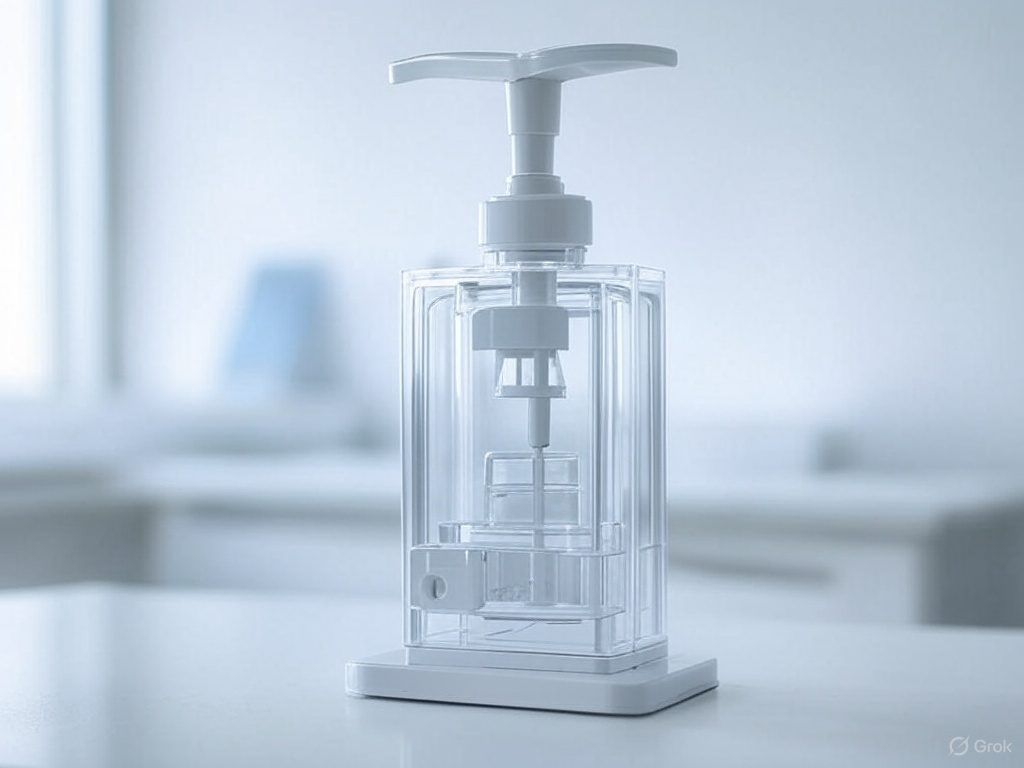
The pump industry has undergone significant advancements in recent years, driven by the need for energy efficiency, smart technology integration, and sustainable operations. Today's cutting-edge pump technologies are transforming industries ranging from water management to oil and gas, offering unprecedented levels of performance and reliability.
Smart Pump Systems and IoT Integration
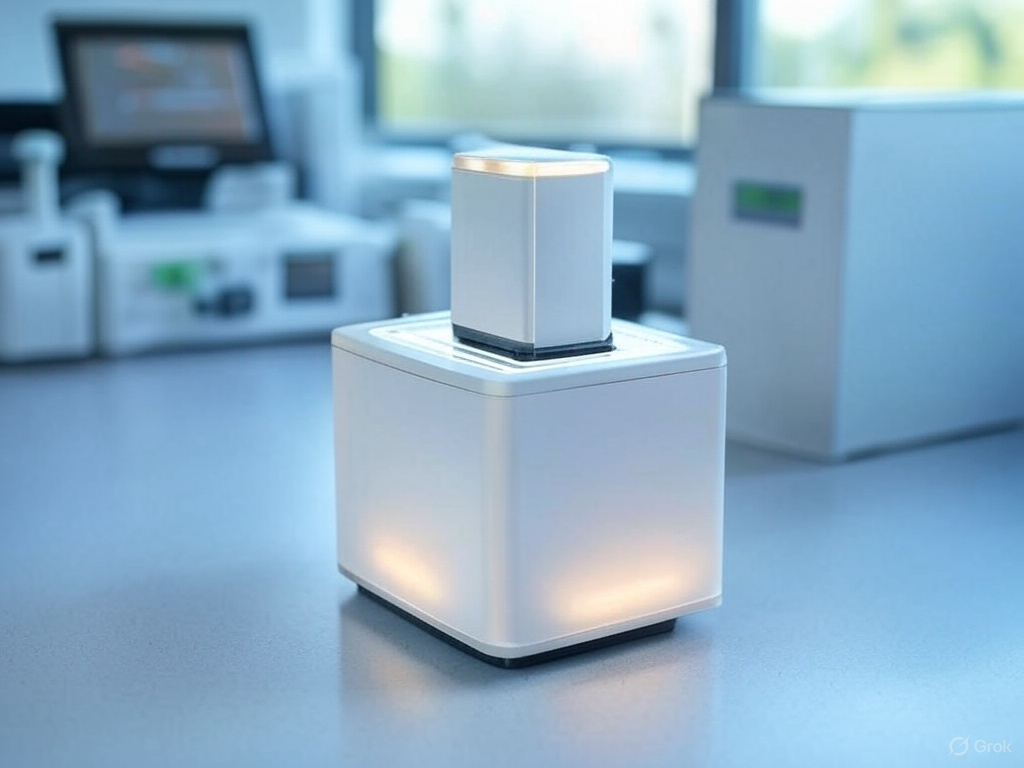
Modern pumps are increasingly equipped with IoT capabilities, allowing for real-time monitoring and predictive maintenance. These smart systems can:
- Detect performance issues before failures occur
- Automatically adjust operations for optimal efficiency
- Provide remote diagnostics and control
- Integrate with building management systems
Leading manufacturers now offer pumps with built-in sensors that track vibration, temperature, pressure, and energy consumption, transmitting this data to cloud platforms for analysis.
Energy-Efficient Pump Designs
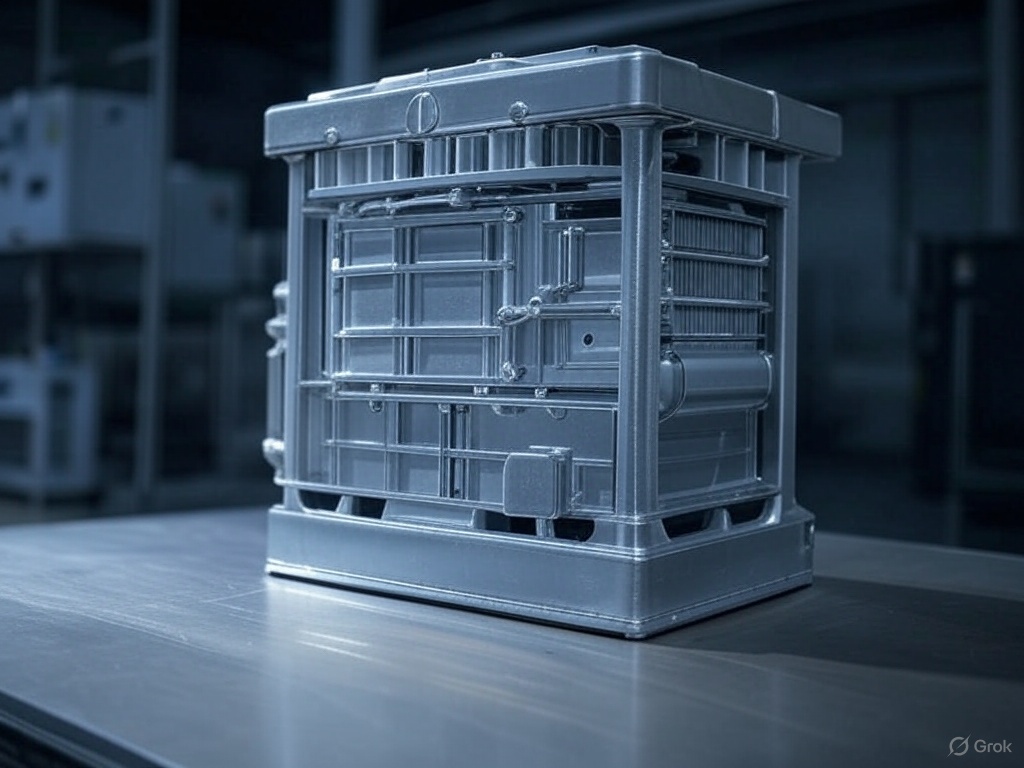
The latest generation of pumps focuses heavily on reducing energy consumption, which typically accounts for 40-60% of a pump's lifecycle costs. Innovations include:
- Variable frequency drives (VFDs) that adjust motor speed to demand
- Improved hydraulic designs reducing internal friction
- High-efficiency permanent magnet motors
- Advanced impeller designs for better fluid dynamics
Some modern pumps achieve energy savings of 30-50% compared to traditional models, with payback periods often under two years.
Magnetic Drive Pumps: Sealing the Future
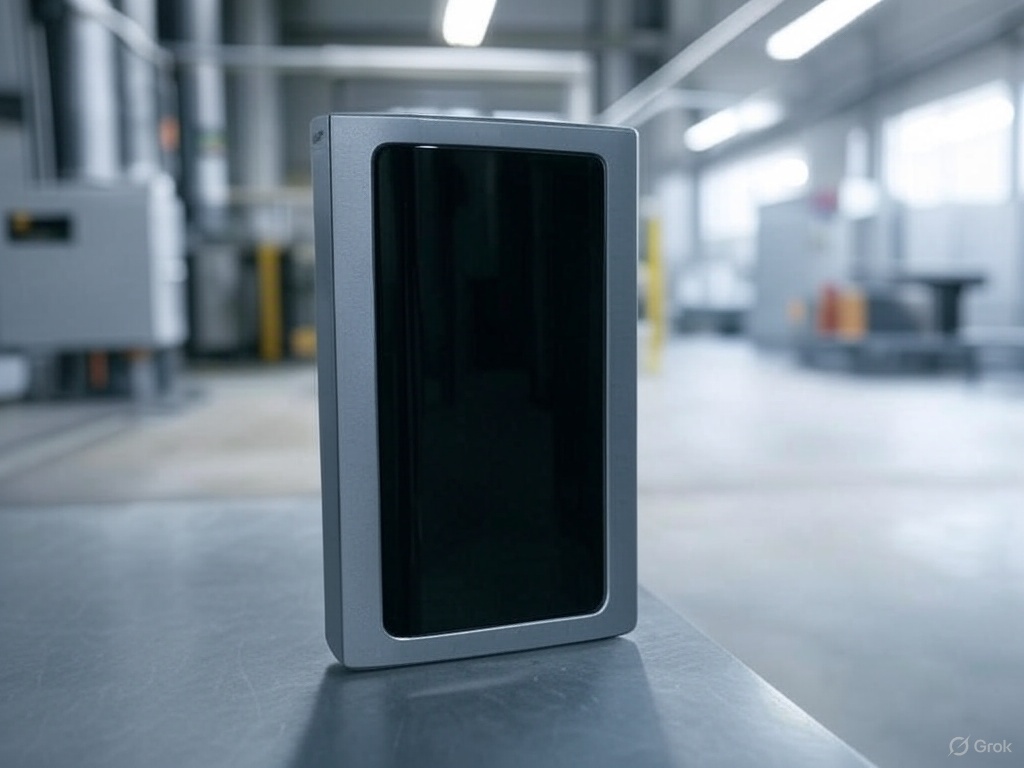
Magnetic drive (mag-drive) pumps represent a major leap forward in sealing technology, eliminating the need for traditional shaft seals that are prone to leakage. Benefits include:
- Zero leakage for handling hazardous or valuable fluids
- Reduced maintenance with no seal replacements
- Improved safety in chemical processing
- Longer service life with proper operation
Recent advancements in magnetic materials have expanded their application to higher pressure and temperature ranges.
3D Printing Revolutionizes Pump Manufacturing
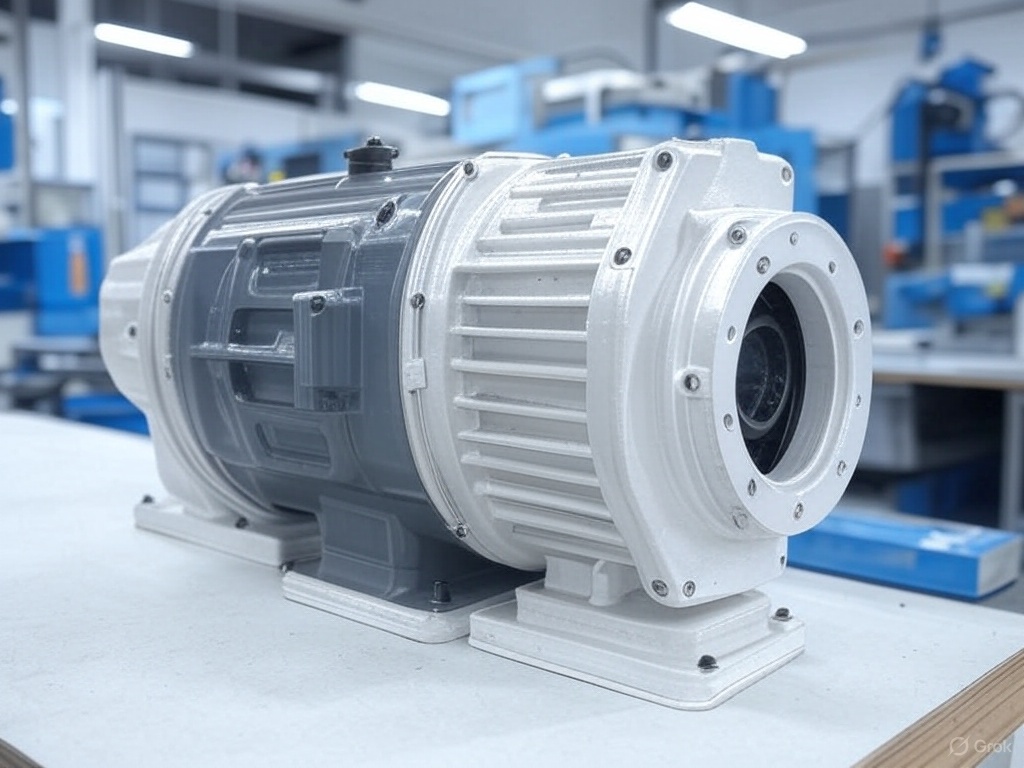
Additive manufacturing is transforming pump production by enabling:
- Complex internal geometries impossible with traditional casting
- Rapid prototyping of new designs
- Customized pumps for specific applications
- Reduced material waste in manufacturing
Several manufacturers now produce 3D-printed metal impellers with optimized hydraulic performance, while others are experimenting with entirely printed pump housings.
Submersible Pump Advancements
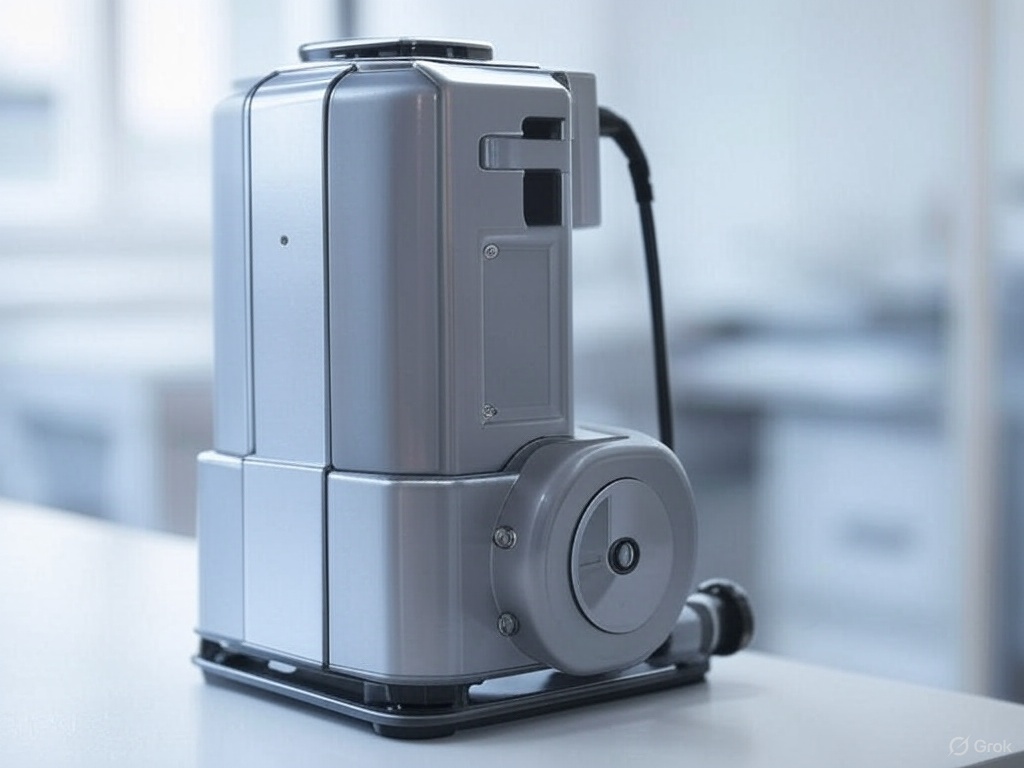
Modern submersible pumps feature significant improvements in:
- Corrosion-resistant materials for longer life
- Improved cooling systems for continuous operation
- Advanced sealing technologies
- Integrated monitoring systems
New designs are handling higher solids content while maintaining efficiency, making them ideal for wastewater and mining applications.
The Future of Pump Technology
Emerging trends that will shape the next generation of pumps include:
- Artificial intelligence for self-optimizing systems
- Nanotechnology coatings to reduce wear
- Biomimetic designs inspired by natural fluid systems
- Advanced materials for extreme environments
- Hydrogen-compatible pumps for the energy transition
As digital transformation continues, pumps will become increasingly connected components within larger smart infrastructure systems.
Conclusion: Pumping Ahead
The pump industry's technological evolution is delivering solutions that are smarter, more efficient, and more reliable than ever before. By adopting these advanced pump technologies, industries can achieve significant cost savings, reduce environmental impact, and improve operational performance. As innovation continues to accelerate, the humble pump is proving to be anything but low-tech in our modern industrial landscape.